塑性:材料变形中的永久形变特性与科学定义解析
adminc2025-05-16app下载2 浏览
在工程和材料科学领域,材料的变形行为直接决定了产品性能和安全性。理解材料在受力后为何会产生不可逆的形变,以及如何通过科学手段预测和控制这种变化,是提升制造工艺和材料设计的核心课题之一。
一、永久形变的本质:弹性与塑性的分界线
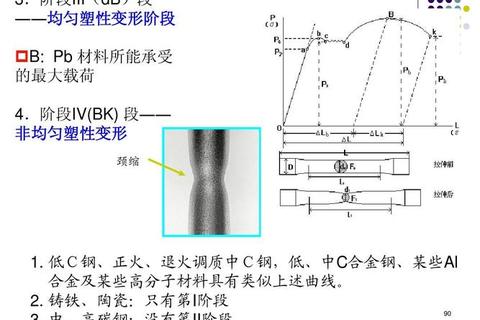
当材料受到外力作用时,其变形可分为两个阶段:弹性变形和塑性变形。
弹性变形:外力移除后,材料能完全恢复原状(例如拉伸弹簧后回弹)。
塑性变形:外力超过临界值时,材料内部结构发生不可逆改变(例如金属被弯折后无法复原)。
科学定义:永久形变即材料在经历塑性变形后保留的残余应变。其产生与原子间的键合方式、晶格滑移、位错运动等微观机制密切相关。例如,金属材料的塑性变形常伴随位错在晶体内的迁移,而高分子材料的塑性则源于分子链的重新排列。
二、影响永久形变的四大关键因素
1. 材料成分与微观结构
金属材料中,晶体结构(如面心立方、体心立方)决定位错移动的难易程度。
高分子材料中,交联密度越高,抗塑性变形能力越强(例如橡胶硫化处理)。
2. 温度条件
高温会降低材料的屈服强度,加速位错运动(如热加工中的锻造工艺)。
低温可能引发脆性断裂(如冬季金属管道的冷脆现象)。
3. 加载速率与应力状态
快速加载可能导致材料来不及发生塑性变形即断裂(冲击载荷下的脆性破坏)。
多轴应力(如拉伸与剪切复合作用)会降低材料的塑性极限。
4. 加工硬化效应
材料在塑性变形过程中因位错堆积而产生强度提升,但延展性降低(例如冷轧钢板)。
三、如何测试与评估永久形变特性
典型测试方法
拉伸试验:通过应力-应变曲线确定屈服强度、断裂延伸率等参数。
硬度测试:间接反映材料抵抗塑性变形的能力(布氏、洛氏硬度标尺)。
循环加载试验:模拟实际工况下的疲劳损伤积累(如弹簧的耐久性测试)。
数据分析要点
屈服点判断:通常取0.2%残余应变对应的应力值作为屈服强度。
应变硬化指数:材料在塑性阶段的强化趋势,影响成型工艺设计。
四、永久形变在工业中的双刃剑作用
有利应用场景
金属成型加工:通过塑性变形制造复杂零件(冲压、锻造)。
结构强化技术:利用加工硬化提升材料表面硬度(喷丸强化处理)。
风险与挑战
尺寸精度失控:塑性变形导致零件尺寸超出公差范围。
疲劳寿命下降:反复塑性应变会加速裂纹萌生(如轴承的接触疲劳)。
五、控制永久形变的实用建议
材料选择策略
高塑性需求场景(如汽车防撞梁):优先选用低屈服强度、高延展性材料(铝合金、低碳钢)。
抗变形需求场景(如机床导轨):选择高强度合金或通过热处理提升硬度。
设计优化方案
避免应力集中:通过圆角过渡、加强筋设计分散载荷。
引入安全系数:根据使用环境留出20%~50%的强度余量。
工艺控制要点
| 工艺类型 | 关键控制参数 |
|-|--|
| 铸造 | 冷却速率、模具预变形补偿 |
| 焊接 | 热输入量、焊后热处理 |
| 3D打印 | 层间温度、扫描路径优化 |
六、未来研究方向与技术突破
多尺度模拟技术:结合分子动力学与有限元分析预测复杂载荷下的塑性行为。
智能材料开发:形状记忆合金在塑性变形后可通过加热恢复原状。
环保工艺革新:低温塑性加工技术减少能源消耗(如液氮辅助切削)。
通过深入理解永久形变的科学本质,并融合跨学科技术手段,人类正不断突破材料的性能极限,为高端制造和可持续发展提供更优解决方案。