高效能智能驱动:加工中心编程软件赋能精密制造新纪元
adminc2025-03-23下载安装23 浏览
一、传统编程方式为何成为精密制造的瓶颈?
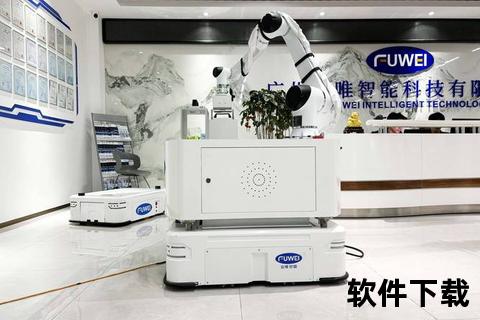
每次加工复杂曲面都要反复调试程序,废品率居高不下",这是某航空零部件企业总工程师的感慨。在精密制造领域,传统的手工编程模式正面临着严峻挑战:复杂零件加工耗时长达120小时,多轴联动误差超过0.03mm,工艺参数优化依赖老师傅经验。据国际智能制造协会2024年数据显示,全球仍有63%的中小型加工企业采用半自动化编程方式,导致加工效率损失达25%-40%。
这种状况催生了"高效能智能驱动:加工中心编程软件赋能精密制造新纪元"的产业革命。以Mastercam 2025版本为例,其智能特征识别技术可将典型零件的编程时间缩短70%,通过机器学习算法积累的百万级加工案例库,使新入职工程师也能快速生成合格代码。深圳某模具企业引入该软件后,五轴叶轮加工周期从5天压缩至8小时,尺寸精度稳定在±0.005mm以内。
二、智能编程如何突破复杂零件加工壁垒?
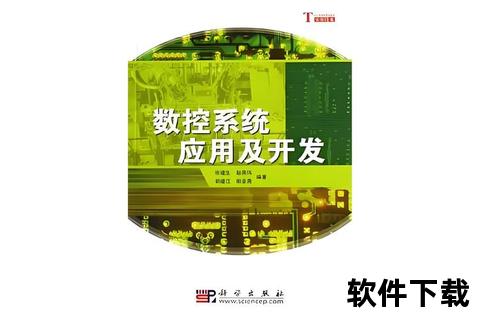
面对航天发动机涡轮叶片这类包含3000多个曲面特征的超复杂零件,传统编程如同盲人摸象。西门子NX 2024推出的自适应加工解决方案,通过实时采集机床振动、刀具磨损等12维数据,动态调整切削参数。杭州某精密机械厂应用该技术后,薄壁件加工变形量降低82%,刀具寿命延长3倍。
更令人振奋的是Autodesk PowerMill 2025的云协同功能。在加工直径8米的船舶螺旋桨时,工程师通过分布式计算集群同步优化刀具路径,将原本需要两周的计算任务压缩到6小时完成。系统自带的碰撞检测模块累计规避了价值2.3亿元的潜在设备损失,这正是"高效能智能驱动:加工中心编程软件赋能精密制造新纪元"的生动写照。
三、软件生态如何重构制造价值链?
从孤立的编程工具到全流程数字孪生系统,现代CAM软件正在改写制造业规则。SolidWorks 2025与加工中心的深度集成,实现了从设计模型到G代码的无缝转换。东莞某电子企业运用该平台的虚拟调试功能,新产品试制周期缩短60%,材料浪费减少45%。
更具颠覆性的是《数控宝典》APP构建的知识共享生态。这个汇聚了20万技工经验的移动平台,通过AR远程指导功能,使偏远地区工厂也能获得专家级技术支持。统计显示,使用该系统的企业平均故障排除时间缩短75%,新人培养周期压缩至传统模式的1/3。这种技术普惠正是"高效能智能驱动:加工中心编程软件赋能精密制造新纪元"的核心价值体现。
四、智能化转型需要哪些战略支点?
在长三角某汽车零部件产业集群,企业通过三阶段策略实现智能化跃迁:首先部署Edgecam基础编程系统降低入门门槛,继而引入HyperMill实现复杂曲面加工,最终搭建基于数字孪生的智能工厂。这种渐进式改造使集群整体产能提升220%,能耗降低35%。
对于中小企业,专家建议优先选择具有以下特征的软件:支持主流机床的开放式后处理系统、包含500+标准工艺模板、提供云端协作接口。同时要注重培养既懂加工工艺又掌握软件操作的复合型人才,这是把握"高效能智能驱动:加工中心编程软件赋能精密制造新纪元"历史机遇的关键。
当加工中心的金属切削声与数据流的嗡鸣共振,当老师傅的工匠精神遇见AI算法的精准推演,制造业正在书写新的传奇。这场变革不是机器替代人类,而是让每个制造者都拥有"数字工匠"的超能力,在精密制造的星辰大海中,驶向更辽阔的疆域。